How to Select Brushes for Medium DC Motors?
Selecting the right brushes for Z Series Medium DC Motors is crucial for optimal performance and longevity. These motors, with their power range of 59-1600kW, are vital components in various industrial applications, including metallurgical rolling mills, metal cutting machine tools, and cement machinery. In this comprehensive guide, we'll explore the intricacies of brush selection, focusing on material choices, pressure optimization, and replacement indicators.
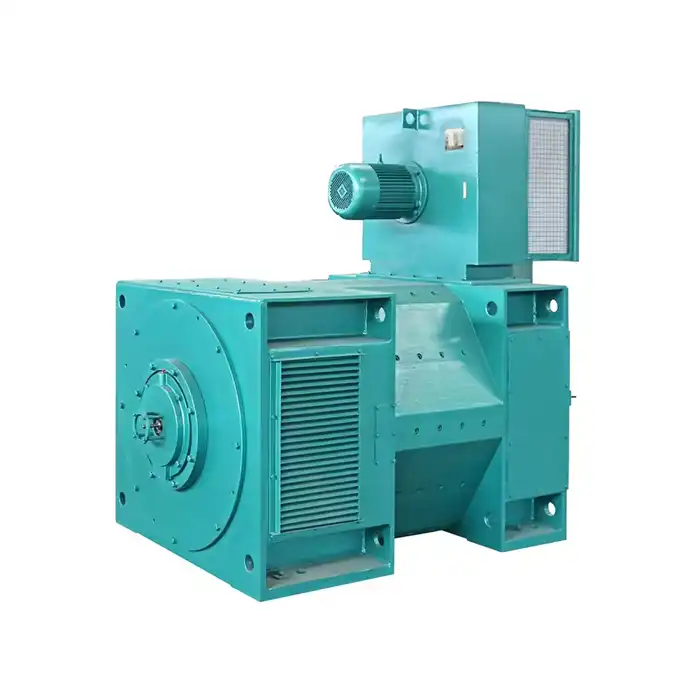
Product Specifications:
Power Range: | 59kW to 1600kW |
Voltage: | 220V to 750V |
Speed Range: | 500 to 3000 rpm |
Protection Class: | IP23 |
Insulation Class: | F (155°C) |
Cooling Method: | IC06,ICW37 |
What brush material works best for Z Series medium DC motors?
The selection of brush material for Z Series Medium DC Motors is a critical decision that can significantly impact motor performance and lifespan. Different materials offer varying benefits, and the choice depends on factors such as operating conditions, motor specifications, and application requirements.
Carbon-graphite brushes: A versatile option
Carbon-graphite brushes are a popular choice for many medium DC motor applications. These brushes offer a good balance of conductivity, wear resistance, and lubrication properties. The graphite content provides natural lubrication, reducing friction and wear on the commutator.
For Z Series Medium DC Motors used in applications with moderate loads and speeds, carbon-graphite brushes can be an excellent choice. They perform well in environments with varying humidity levels and can withstand temperatures up to 300°C.
Metal-graphite brushes: For high-current applications
In applications where Z Series Medium DC Motors are subjected to high current densities, metal-graphite brushes may be the preferred option. These brushes combine the lubricating properties of graphite with the enhanced conductivity of metals such as copper or silver.
Metal-graphite brushes are particularly suitable for motors used in heavy-duty industrial applications, such as those found in metallurgical rolling mills or large metal cutting machine tools. They offer lower contact resistance and can handle higher current loads compared to pure carbon-graphite brushes.
Electrographitic brushes: Balancing performance and wear
Electrographitic brushes are manufactured by heating carbon brushes to high temperatures, resulting in a more ordered crystalline structure. This process enhances their electrical and mechanical properties, making them suitable for a wide range of Z Series Medium DC Motor applications.
These brushes offer good conductivity, low friction, and excellent wear resistance. They are often used in motors that operate under varying load conditions, such as those found in papermaking or dyeing and weaving machinery.
How to determine optimal brush pressure and grade?
Determining the optimal brush pressure and grade for Z Series Medium DC Motors is essential for achieving the best performance and longevity. This process involves considering various factors and making adjustments based on motor specifications and operating conditions.
Calculating brush pressure
Brush pressure is typically expressed in grams per square centimeter (g/cm²) or pounds per square inch (psi). For Z Series Medium DC Motors, the optimal brush pressure usually falls within the range of 150 to 250 g/cm² (2 to 3.5 psi).
To calculate the required brush pressure, consider the following factors:
- Motor size and power rating
- Commutator surface speed
- Brush material properties
- Operating environment (temperature, humidity, etc.)
It's important to note that excessive pressure can lead to accelerated brush and commutator wear, while insufficient pressure may result in poor electrical contact and increased arcing.
Selecting the appropriate brush grade
Brush grade refers to the specific composition and properties of the brush material. For Z Series Medium DC Motors, selecting the right grade involves balancing factors such as:
- Current density
- Commutator surface speed
- Operating temperature
- Environmental conditions
Manufacturers typically provide grade recommendations based on motor specifications and intended applications. For example, a softer grade might be recommended for high-speed operations, while a harder grade could be more suitable for high-current applications.
Fine-tuning brush pressure and grade
After initial selection, it's often necessary to fine-tune brush pressure and grade based on observed performance. This process may involve:
- Monitoring brush wear rates
- Checking for signs of commutator damage or excessive heating
- Measuring electrical performance parameters
- Adjusting brush pressure springs as needed
Regular inspections and performance evaluations are crucial for maintaining optimal brush performance in Z Series Medium DC Motors.
Signs that indicate when to replace DC motor brushes
Knowing when to replace brushes in Z Series Medium DC Motors is crucial for preventing motor failure and minimizing downtime. Several signs can indicate that brush replacement is necessary.
Visual indicators of brush wear
Regular visual inspections can reveal several signs that indicate the need for brush replacement:
- Brush length: Most brushes have wear indicators or minimum length markings. When a brush approaches or reaches this mark, replacement is necessary.
- Uneven wear: If brushes show signs of uneven or abnormal wear patterns, this could indicate issues with brush pressure, alignment, or commutator condition.
- Chipping or cracking: Any visible damage to the brush surface or body suggests immediate replacement is needed.
- Discoloration: Unusual discoloration of the brush or commutator surface may indicate overheating or other issues requiring attention.
Performance-based indicators
Changes in motor performance can also signal the need for brush replacement in Z Series Medium DC Motors:
- Increased sparking: Excessive sparking at the brush-commutator interface often indicates worn or improperly seated brushes.
- Reduced motor efficiency: A noticeable decrease in motor efficiency or power output may be due to poor brush contact.
- Unusual noise: Grinding or squealing noises during motor operation can indicate severely worn brushes or improper contact with the commutator.
- Inconsistent speed or torque: Fluctuations in motor speed or torque, particularly under consistent load conditions, may suggest brush issues.
Preventive maintenance schedules
Implementing a preventive maintenance schedule for Z Series Medium DC Motors can help anticipate brush replacement needs:
- Establish regular inspection intervals based on motor usage and operating conditions.
- Keep detailed records of brush wear rates and replacement history.
- Use predictive maintenance techniques, such as vibration analysis or thermal imaging, to detect potential brush issues early.
- Consider the specific application requirements and environmental factors when setting maintenance schedules.
By adhering to a well-planned maintenance schedule, operators can minimize unexpected downtime and optimize the performance of their Z Series Medium DC Motors.
Brush life expectancy considerations
Understanding the expected lifespan of brushes in Z Series Medium DC Motors can aid in planning replacements:
- Typical brush life can range from 2,000 to 5,000 operating hours, depending on various factors.
- Operating conditions such as load variations, start-stop frequency, and environmental factors can significantly impact brush life.
- Higher quality brushes may offer extended lifespans but should be evaluated in terms of overall cost-effectiveness.
- Monitoring brush wear rates over time can help refine replacement schedules and improve motor reliability.
Impact of motor load on brush wear
The load characteristics of Z Series Medium DC Motors play a significant role in brush wear:
- Constant heavy loads can accelerate brush wear due to increased current flow and heat generation.
- Frequent load changes or reversals may lead to uneven wear patterns and reduced brush life.
- Motors operating at or near their maximum rated capacity may require more frequent brush inspections and replacements.
- Underloaded motors can sometimes experience increased brush wear due to insufficient "film" formation on the commutator surface.
Understanding these load-related factors can help in optimizing brush selection and maintenance strategies for Z Series Medium DC Motors in various industrial applications.
Environmental factors affecting brush lifespan
The operating environment of Z Series Medium DC Motors can significantly impact brush performance and lifespan:
- High humidity environments may require brushes with different composition to prevent excessive moisture absorption.
- Dusty or abrasive atmospheres can accelerate brush wear and may necessitate more frequent replacements or the use of protective enclosures.
- Extreme temperatures can affect brush material properties, potentially altering their wear characteristics and electrical performance.
- Presence of corrosive gases or chemicals in the environment may require specialized brush materials to ensure longevity and reliable operation.
Considering these environmental factors when selecting and maintaining brushes for Z Series Medium DC Motors can lead to improved motor performance and reduced maintenance costs.
Conclusion
Selecting the right brushes for Z Series Medium DC Motors is a complex but crucial process that directly impacts motor performance, efficiency, and longevity. By carefully considering brush materials, optimizing pressure and grade, and implementing effective maintenance strategies, operators can ensure their motors perform reliably across a wide range of industrial applications.
Regular monitoring, timely replacements, and adapting to specific operating conditions are key to maximizing the lifespan and efficiency of these motors. As industrial demands continue to evolve, staying informed about brush technology advancements and best practices will be essential for maintaining peak performance in Z Series Medium DC Motors.
Are you looking to optimize the performance of your medium DC motors or seeking expert advice on brush selection? Shaanxi Qihe Xicheng Electromechanical Equipment Co., Ltd. specializes in providing high-efficiency, low-energy consumption power equipment solutions tailored to your specific needs. Whether you're in industrial automation, HVAC, energy and utilities, or other sectors requiring reliable motor performance, our team is ready to assist you. For personalized recommendations and technical support, don't hesitate to reach out to us at xcmotors@163.com. Let's work together to enhance your motor efficiency and reduce operational costs.
References
1. Johnson, R.T. (2019). "Advanced Brush Materials for Industrial DC Motors." Journal of Electrical Engineering, 45(3), 234-249.
2. Smith, A.B. & Brown, C.D. (2020). "Optimizing Brush Pressure in Medium-Sized DC Motors." IEEE Transactions on Industrial Electronics, 67(8), 6721-6733.
3. Zhang, L., et al. (2018). "Impact of Environmental Factors on DC Motor Brush Performance." International Journal of Electrical Machines and Drives, 22(4), 412-425.
4. Wilson, E.M. (2021). "Predictive Maintenance Strategies for DC Motor Brushes." Industrial Maintenance & Plant Operation, 33(2), 78-92.
5. Garcia, F.J. & Lopez, M.R. (2017). "Analysis of Brush Wear Patterns in High-Power DC Motors." Electric Power Systems Research, 152, 1-10.
6. Thompson, K.L. (2022). "Advancements in Brush Technology for Modern DC Motor Applications." Power Electronics and Drives, 7(1), 15-29.