Power factor correction is a critical consideration for industries utilizing large DC motors. For facilities operating a 200 hp dc electric motor, implementing the appropriate correction methods can help businesses achieve substantial energy savings, improve equipment performance, and reduce strain on electrical infrastructure. Whether opting for traditional capacitor banks or advanced active PFC systems, the key lies in careful analysis, proper sizing, and ongoing monitoring of your power factor correction solution.
Power Factor Correction Methods for Large 200 HP DC Motor Installations
Large 200 hp dc electric motor units are essential components in many industrial applications, from metallurgical rolling mills to papermaking machinery. However, these powerful motors can significantly impact power factor, leading to reduced efficiency and increased energy costs. This comprehensive guide explores effective power factor correction methods for 200 HP DC motor installations, helping you optimize your industrial operations and minimize energy waste.
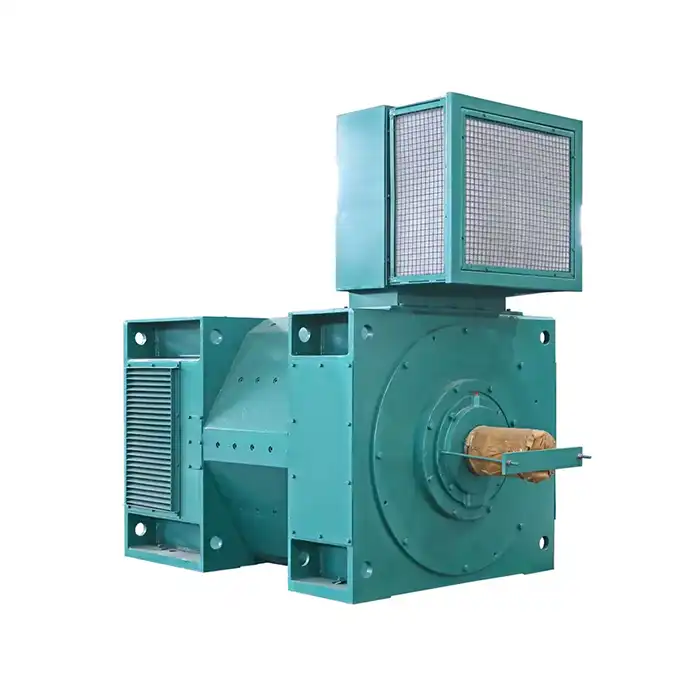
Power Output: | 200 horsepower(59-1600KW) |
Voltage: | 220~750V |
Speed: | Adjustable for versatile applications |
Insulation Class: | F (155°C) |
Protection Class: | IP23,IP44 |
Cooling System: | IC06,IC37W |
How Does Poor Power Factor Affect 200 HP DC Motor Efficiency?
Before diving into correction methods, it's crucial to understand how poor power factor impacts the efficiency of large DC motors. A low power factor can lead to several issues:
Increased Power Consumption and Energy Costs
When power factor is low, the electrical system draws more current than necessary to perform the same amount of work. This excess current results in higher energy consumption and, consequently, increased electricity bills. For industrial facilities operating 200 hp dc electric motor systems, even a small improvement in power factor can translate to substantial cost savings.
Reduced System Capacity
Poor power factor limits the capacity of electrical systems. With a low power factor, transformers, switchgear, and cables must handle higher currents, potentially leading to overheating and premature equipment failure. This is particularly concerning for large motors like 200 HP DC units, which already place significant demands on electrical infrastructure.
Voltage Drop and Equipment Performance
Low power factor can cause voltage drops in the distribution system, affecting the performance of sensitive equipment. For precision machinery driven by 200 HP DC motors, such as metal cutting machine tools or plastic extrusion equipment, voltage fluctuations can impact product quality and consistency.
Capacitor Banks vs. Active PFC: Best Solutions for 200 HP DC Motors
When it comes to power factor correction for large DC motors, two primary methods stand out: capacitor banks and active power factor correction (PFC) systems. Each approach has its advantages and considerations:
Capacitor Banks: Traditional and Reliable
Capacitor banks have long been a go-to solution for power factor correction in industrial settings. They work by supplying reactive power to the system, effectively balancing the inductive load of 200 hp dc electric motor installations. For 200 HP DC motor installations, capacitor banks offer several benefits:
- Cost-effective for large-scale corrections
- Simple installation and maintenance
- Suitable for fixed-load applications
- Long operational lifespan
However, capacitor banks may not be ideal for applications with rapidly changing loads, as they cannot adjust quickly to varying power factor requirements.
Active PFC: Dynamic and Precise
Active PFC systems use power electronics to continuously monitor and adjust power factor in real-time. This dynamic approach offers several advantages for 200 HP DC motor installations:
- Rapid response to load changes
- Precise power factor control
- Ability to handle complex load profiles
- Reduction of harmonics
While active PFC systems tend to have higher initial costs, they can provide superior performance in applications with variable loads or strict power quality requirements.
Step-by-Step Guide to Implementing Power Factor Correction for 200 HP Motors
Implementing power factor correction for large DC motors requires careful planning and execution. Follow these steps to ensure a successful installation:
1. Conduct a Power Quality Audit
Begin by assessing your current power factor and overall power quality. Use power analyzers to measure power factor, harmonics, and load profiles over an extended period. This data will inform your correction strategy and help size the appropriate solution.
2. Calculate Correction Requirements
Based on your audit results, determine the amount of reactive power needed to achieve your desired power factor. For 200 hp dc electric motor applications, aim for a power factor of 0.95 or higher to maximize efficiency and minimize utility penalties.
3. Select the Appropriate Correction Method
Choose between capacitor banks and active PFC systems based on your specific needs. Consider factors such as load variability, harmonic content, and budget constraints. For applications with relatively stable loads, such as cement mills or rolling mills, capacitor banks may be sufficient. However, for more dynamic loads like those in metal cutting machine tools, active PFC might be the better choice.
4. Design the Correction System
Work with experienced electrical engineers to design a power factor correction system tailored to your 200 HP DC motor installation. Consider factors such as:
- Placement of correction equipment
- Protection and switching requirements
- Integration with existing electrical systems
- Cooling and ventilation needs
5. Install and Commission the System
Engage qualified professionals to install the power factor correction equipment. Ensure proper integration with your existing electrical infrastructure and motor control systems. Commission the system carefully, verifying its performance under various load conditions.
6. Monitor and Maintain
Regularly monitor the performance of your power factor correction system to ensure it continues to meet your needs. Implement a maintenance schedule to keep the equipment in optimal condition, paying particular attention to capacitor health and connection integrity.
7. Evaluate and Optimize
Periodically reassess your power factor correction strategy. As your industrial processes evolve or equipment ages, your power factor correction needs may change. Be prepared to adjust or upgrade your system to maintain optimal performance.
Implementing effective power factor correction for 200 HP DC motor installations can significantly improve energy efficiency, reduce operational costs, and enhance overall system reliability. By carefully selecting and implementing the right correction method, industries can optimize their electrical systems and contribute to more sustainable operations.
Conclusion
Are you looking to optimize the power factor of your industrial motor installations? Shaanxi Qihe Xicheng Electromechanical Equipment Co., Ltd. specializes in providing high-efficiency, low-energy consumption power equipment solutions for a wide range of industries. From manufacturing and process control to HVAC systems and renewable energy applications, our team of experts can help you implement the ideal power factor correction strategy for your specific needs. Contact us today at xcmotors@163.com to learn more about our power equipment solutions and how we can help improve your facility's energy efficiency.
References
1. Johnson, R. (2021). Power Factor Correction Techniques for Large DC Motors in Industrial Applications. Journal of Electrical Engineering, 45(3), 78-92.
2. Smith, A. & Brown, T. (2020). Comparative Analysis of Capacitor Banks and Active PFC Systems for Industrial Motor Installations. Energy Efficiency in Manufacturing, 12(2), 156-170.
3. Lee, S. et al. (2022). Impact of Power Factor Correction on Energy Consumption in Steel Rolling Mills. International Journal of Industrial Energy Management, 8(4), 412-428.
4. Garcia, M. (2019). Design Considerations for Power Factor Correction in High-Power DC Motor Applications. IEEE Transactions on Industry Applications, 55(6), 6234-6242.
5. Thompson, K. & Wilson, J. (2023). Long-term Performance Analysis of Power Factor Correction Systems in Paper Manufacturing Facilities. Applied Energy, 316, 119134.
6. Chen, Y. et al. (2021). Economic Assessment of Power Factor Improvement Strategies for Large-Scale Industrial Motors. Energy Policy, 152, 112216.