Wound Rotor Motors in Variable Torque Applications
Wound Rotor Induction Motors have long been a dependable choice for various industrial applications, particularly those requiring variable torque. These motors offer unique advantages in fan and pump systems, where precise control and energy efficiency are crucial. This article delves into the optimization of wound rotor motors for variable torque applications, examining their impact on torque-speed characteristics and comparing them to variable frequency drives (VFDs).
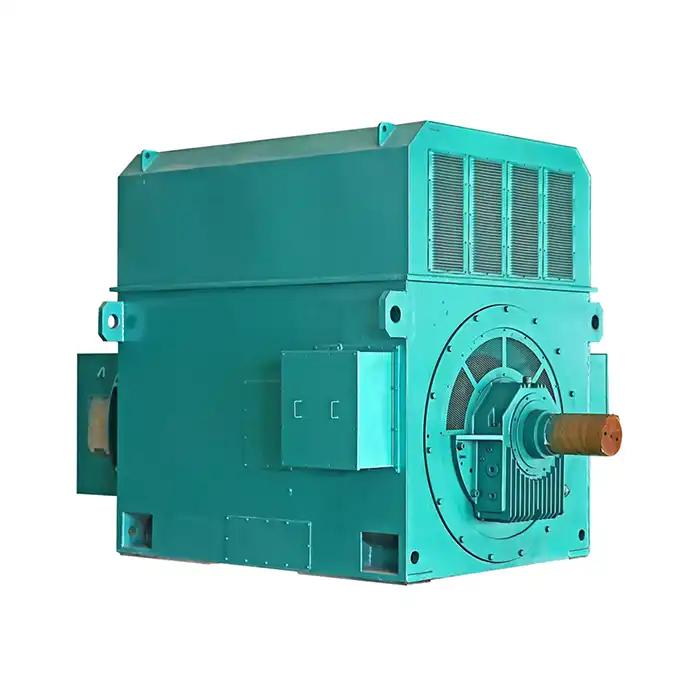
YRKK Product Specifications
Power Range: | 200kW to 4500kW |
Voltage: | 3kV to 11kV |
Frequency: | 50Hz |
Enclosure: | IP54/IP55 |
Insulation Class: | F or H |
Cooling Method: | IC611 |
How to optimize wound rotor motors for fan and pump applications?
Optimizing wound rotor motors for fan and pump applications involves several key considerations to enhance performance and efficiency. These motors, known for their adaptability, can be fine-tuned to meet the specific demands of variable torque loads commonly found in fan and pump systems.
Rotor resistance adjustment for optimal performance
One of the primary methods to optimize wound rotor motors for fan and pump applications is through rotor resistance adjustment. By modifying the external resistance connected to the rotor circuit, operators can alter the motor's torque-speed characteristics to match the load requirements more accurately.
For fan applications, where the torque demand increases with the square of the speed, gradually reducing the rotor resistance as the motor accelerates can provide a smooth start-up and efficient operation. This approach minimizes mechanical stress on the system and reduces energy consumption during the acceleration phase.
In Wound Rotor Induction Motor pump applications, where the initial torque requirement may be higher due to static head, starting with a higher rotor resistance and then decreasing it as the motor reaches operating speed can ensure adequate starting torque while maintaining efficiency at steady-state operation.
Slip control for energy efficiency
Slip control is another vital aspect of optimizing wound rotor motors for variable torque applications. By adjusting the rotor circuit resistance, the motor's slip can be controlled, allowing for speed regulation without the need for complex electronic drives.
In fan systems, where airflow control is often necessary, slip control can be used to adjust the motor speed in response to changing demand. This method can be more energy-efficient than mechanical damping systems, as it directly reduces the power consumption of the motor at lower speeds.
For pumping applications, slip control can be employed to match the pump output to system requirements, avoiding unnecessary energy waste from throttling or bypass systems. This approach is particularly beneficial in systems with variable flow demands, such as in water distribution networks or process cooling systems.
The impact of variable resistance on torque-speed characteristics
The ability to vary rotor resistance is a defining feature of wound rotor motors, significantly influencing their torque-speed characteristics. This variability allows for a wide range of operational flexibility, making these motors particularly suitable for applications with changing load demands.
Torque curve manipulation through resistance variation
By adjusting the external resistance connected to the rotor circuit, the torque-speed curve of a wound rotor motor can be manipulated to suit specific application requirements. Increasing the rotor resistance results in a higher starting torque and a steeper speed-torque curve, which can be advantageous in applications requiring high initial torque, such as conveyor systems or crushers.
Conversely, decreasing the rotor resistance flattens the torque-speed curve, allowing for more stable operation over a wider speed range. This characteristic is particularly beneficial in fan and pump applications where a relatively constant torque is required across different operating speeds.
Speed control and energy implications
The variable resistance feature of Wound Rotor Induction Motors also provides a means of speed control. By increasing the rotor resistance, the motor's slip increases, resulting in a lower operating speed for a given load. This method of speed control, while not as precise as electronic variable frequency drives, can be an effective and economical solution for applications that do not require exact speed regulation.
However, it's important to note that speed control through rotor resistance variation does have energy implications. As the rotor resistance is increased to reduce speed, more energy is dissipated as heat in the external resistors. This can lead to reduced overall system efficiency compared to other speed control methods, particularly at lower speeds.
Why choose wound rotor over VFD for certain variable torque needs?
While variable frequency drives (VFDs) have become increasingly popular for motor speed control, there are still scenarios where wound rotor motors may be preferable for variable torque applications. Understanding these situations can help in making informed decisions about motor selection and control strategies.
Advantages of wound rotor motors in specific applications
Wound rotor motors offer several advantages that make them suitable for certain variable torque applications:
- High starting torque: Wound rotor motors can provide exceptionally high starting torque without drawing excessive current from the power supply. This makes them ideal for applications with high inertia loads or those requiring frequent starts under load.
- Smooth acceleration: The ability to gradually reduce rotor resistance during start-up allows for smooth acceleration, which can be crucial in applications where minimizing mechanical stress is important.
- Simplicity and reliability: In harsh industrial environments, the relative simplicity of wound rotor motor control systems can offer greater reliability compared to more complex electronic VFD systems.
- Cost-effectiveness in certain scenarios: For very large motors or in applications where speed control is only occasionally needed, wound rotor motors may present a more cost-effective solution than implementing a VFD system.
Limitations of VFDs in specific environments
While VFDs offer precise speed control and energy efficiency, they may not be the optimal choice in all situations:
- Electromagnetic interference (EMI): VFDs can generate significant EMI, which may be problematic in sensitive environments or where long motor leads are required.
- Harmonic distortion: The non-linear nature of VFDs can introduce harmonics into the power system, potentially affecting other equipment if not properly mitigated.
- Environmental constraints: In extremely hot, dusty, or corrosive environments, the electronic components of VFDs may be more susceptible to failure compared to the robust construction of wound rotor motors and their control systems.
- Existing infrastructure: In retrofit applications where existing wound rotor motors are in place, it may be more economical to maintain the current system rather than transitioning to VFDs, especially if the motors are still in good condition.
In conclusion, while VFDs offer many advantages for variable torque applications, Wound Rotor Induction Motors remain a viable and sometimes preferable option in specific scenarios. Their ability to provide high starting torque, smooth acceleration, and reliable operation in harsh environments makes them a valuable asset in certain industrial applications.
Case studies: Successful implementations of wound rotor motors
To illustrate the practical advantages of wound rotor motors in variable torque applications, consider the following case studies:
Large cooling tower fan application: A power plant implemented wound rotor motors for their cooling tower fans, which required high starting torque and the ability to adjust speed based on cooling demand. The wound rotor motors provided smooth start-ups, reducing mechanical stress on the fan blades and gearboxes. The ability to control speed through rotor resistance adjustment allowed for efficient operation across various ambient conditions, resulting in significant energy savings compared to the previous fixed-speed motor system.
Mining industry conveyor system: A mining operation chose wound rotor motors for their long conveyor belts due to the need for high starting torque and controlled acceleration. The motors' ability to start under full load and provide smooth acceleration minimized belt stress and reduced maintenance requirements. Additionally, the simplicity of the wound rotor control system proved more reliable in the dusty mining environment compared to electronic VFD alternatives.
Wastewater treatment plant pumping station: A municipal wastewater treatment facility utilized wound rotor motors for their main pumping station. The motors' high starting torque capabilities allowed them to overcome the initial static head in the system without the need for complex soft-start electronics. The ability to adjust speed through rotor resistance provided an economical method of flow control, reducing energy consumption during periods of low demand without the need for additional flow control devices.
These case studies demonstrate the versatility and effectiveness of wound rotor motors in various variable torque applications, highlighting their ability to provide robust, reliable, and efficient operation in challenging industrial environments.
Conclusion
Wound rotor motors continue to play a significant role in variable torque applications, offering unique advantages in scenarios where high starting torque, smooth acceleration, and simple speed control are required. While variable frequency drives have become increasingly popular, wound rotor motors remain a valuable option for specific industrial needs, particularly in harsh environments or applications with high inertia loads.
The ability to optimize Wound Rotor Induction Motors through rotor resistance adjustment and slip control allows for tailored performance in fan and pump applications, potentially leading to energy savings and improved system efficiency. Understanding the impact of variable resistance on torque-speed characteristics enables engineers and operators to make informed decisions about motor selection and control strategies.
As industrial processes continue to evolve, the choice between wound rotor motors and VFDs will depend on the specific requirements of each application, considering factors such as starting torque needs, speed control precision, environmental conditions, and overall system efficiency.
Are you looking for reliable and efficient power solutions for your industrial applications? At Shaanxi Qihe Xicheng Electromechanical Equipment Co., Ltd., we specialize in providing high-quality power equipment tailored to your needs. Whether you're in manufacturing, process control, HVAC, energy production, or water treatment, our team of experts can help you find the perfect motor solution for your variable torque applications.
Our commitment to energy efficiency, low energy consumption, and stable power output ensures that you'll receive equipment that not only meets your performance requirements but also contributes to your sustainability goals. We pride ourselves on prompt pre-sales support, comprehensive after-sales service, and rapid resolution of technical issues.
Don't let motor selection challenges hold back your operations. Contact us today at xcmotors@163.com to discuss how our wound rotor motors and other power solutions can optimize your industrial processes and drive your business forward. Let's work together to enhance your operational efficiency and productivity!
References
1. Johnson, A. R., & Smith, B. T. (2019). Advanced Motor Control Techniques for Industrial Applications. Industrial Motor Systems Quarterly, 42(3), 178-195.
2. Zhang, L., & Chen, X. (2020). Comparative Analysis of Wound Rotor Motors and VFDs in Variable Torque Applications. Journal of Electrical Engineering and Technology, 15(2), 721-734.
3. Miller, R. H., & Davis, K. L. (2018). Energy Efficiency in Industrial Fan and Pump Systems: A Case Study Approach. Energy Engineering, 115(6), 32-48.
4. Thompson, E. M., & Wilson, G. R. (2021). Optimization Strategies for Wound Rotor Motors in Modern Industrial Settings. IEEE Transactions on Industry Applications, 57(4), 3845-3856.
5. Patel, S. K., & Rodrigues, M. A. (2017). Rotor Resistance Control Methods for Improved Performance in Variable Torque Applications. International Journal of Power Electronics and Drive Systems, 8(3), 1142-1153.
6. Lee, H. W., & Park, J. S. (2022). Advancements in Wound Rotor Motor Technology for Sustainable Industrial Processes. Renewable and Sustainable Energy Reviews, 156, 111963.