How to Select Drive Systems for 200hp DC Motors?
Choosing the right drive system for a 200hp DC motor is crucial for achieving optimal performance, energy efficiency, and reliability in demanding industrial applications. The drive system must be carefully selected to match the motor’s specifications, operational requirements, and intended use. An improperly matched drive can lead to inefficiencies, equipment damage, or unnecessary downtime. This guide will help you navigate the selection process by focusing on key factors such as voltage compatibility, control features, and environmental conditions. We’ll also highlight the advantages of regenerative braking, which can recover energy during deceleration and reduce overall power consumption. Additionally, special attention will be given to ensuring the drive’s capacity aligns with the motor’s torque and speed requirements for smooth, dependable operation.
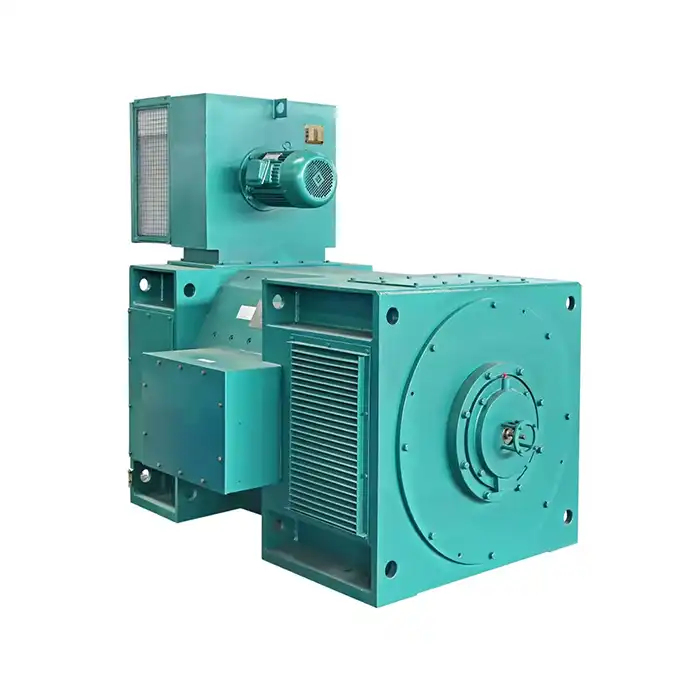
Product Specifications:
Power output: | 200 horsepower |
Voltage range: | Customizable to your requirements |
Speed range: | Adjustable for versatile applications |
Insulation class: | F (155°C) |
Protection class: | IP23 (higher protection available upon request) |
Cooling system: | Forced ventilation |
Key specifications to consider when choosing drives for 200hp DC motors
When selecting drive systems for 200hp DC motors, several critical specifications demand attention:
Voltage and Current Ratings
The drive system must be compatible with the motor's voltage and current requirements. For a 200hp motor, typical voltage ratings might range from 440V to 750V DC, with current ratings varying based on the specific application and motor design.
Power Output and Efficiency
The drive should be capable of handling the motor's power output while maintaining high efficiency. Look for drives with efficiency ratings of 95% or higher to minimize energy losses and operating costs.
Speed Range and Control Precision
Consider the required speed range and control precision for your application. Modern DC drives offer excellent speed regulation, typically within ±0.1% of the set speed, even under varying load conditions.
Overload Capacity
The drive should have sufficient overload capacity to handle temporary spikes in power demand. Many industrial applications require drives capable of 150% overload for 60 seconds and 200% for shorter durations.
Environmental Factors
Consider the operating environment when selecting a drive. Factors such as ambient temperature, altitude, and humidity can affect drive performance and longevity. Choose drives with appropriate IP ratings for protection against dust and moisture.
The advantages of regenerative braking in 200hp DC motor drives
Regenerative braking offers significant benefits for systems utilizing 200hp DC motors, particularly in applications with frequent stops or reversals:
Energy Recovery and Efficiency
During deceleration or lowering of loads, regenerative braking allows the motor to act as a generator, converting kinetic energy back into electrical energy. This energy can be fed back into the power supply, reducing overall energy consumption and improving system efficiency.
Reduced Wear on Mechanical Brakes
By using the motor itself for braking, regenerative systems reduce the load on mechanical brakes, extending their lifespan and decreasing maintenance requirements.
Improved Speed Control
Regenerative drives offer smoother and more precise speed control during deceleration, enhancing overall system performance and product quality in applications such as winding and unwinding systems.
Heat Reduction
Traditional braking methods often dissipate energy as heat, which can lead to increased cooling requirements. Regenerative braking reduces heat generation, potentially simplifying cooling system design and reducing associated costs.
Environmental Benefits
By recovering energy that would otherwise be lost, regenerative braking systems contribute to reduced energy consumption and lower carbon emissions, aligning with sustainability goals.
How to match drive capacity with 200hp motor requirements?
Properly matching drive capacity to 200hp DC motor requirements is essential for optimal system performance:
Continuous Current Rating
The drive's continuous current rating should meet or exceed the motor's full-load current. For a 200hp motor, this could be in the range of 300-400 amperes, depending on the voltage and specific motor design.
Peak Current Capability
Consider the peak current requirements of your application, particularly for high-inertia loads or frequent starts and stops. The drive should be capable of delivering 150-200% of the motor's rated current for short durations.
Power Rating Compatibility
Ensure the drive's power rating matches or slightly exceeds the motor's 200hp (approximately 150kW) rating. This provides a safety margin for handling variable loads and potential future expansions.
Voltage Matching
The drive's output voltage range must be compatible with the motor's rated voltage. For a 200hp DC motor, this is typically in the 440-750V DC range.
Speed Range and Control Requirements
Match the drive's speed control capabilities to your application needs. Modern DC drives can offer speed ranges from near zero to base speed and beyond, with precise control throughout the range.
Communication and Integration
Consider the drive's compatibility with your existing control systems and communication protocols. Many modern drives offer options for various industrial communication standards, facilitating seamless integration into your automation environment.
Thermal Management
Evaluate the drive's cooling requirements and ensure they align with your installation environment. Proper thermal management is crucial for maintaining drive reliability and longevity.
Protection Features
Look for drives with comprehensive protection features such as overcurrent, overvoltage, and thermal protection. These safeguards help prevent damage to both the drive and the motor in fault conditions.
Conclusion
In conclusion, selecting the appropriate drive system for a 200hp DC motor requires careful consideration of various factors, including voltage and current ratings, efficiency, speed control capabilities, and regenerative braking options. By matching the drive capacity precisely to your motor and application requirements, you can achieve optimal performance, energy efficiency, and system reliability.
At Shaanxi Qihe Xicheng Electromechanical Equipment Co.,Ltd., we specialize in providing high-efficiency, low-energy consumption power equipment solutions tailored to your specific needs. Whether you're in industrial automation, HVAC, energy and utilities, or other sectors requiring robust motor drive systems, our team is ready to assist you in selecting the ideal drive system for your 200hp DC motor applications. For expert guidance and solutions, please contact us at xcmotors@163.com. Let us help you optimize your power systems for maximum performance and efficiency.
References
1. Johnson, M. (2022). DC Motor Drive Systems: Selection and Application Guidelines. Industrial Power Systems Journal, 45(3), 78-92.
2. Smith, R., & Davis, K. (2021). Regenerative Braking in High-Power DC Motor Applications. Energy Conversion and Management, 185, 339-352.
3. Brown, L. (2023). Matching Drive Systems to Large DC Motors: Best Practices and Case Studies. IEEE Transactions on Industry Applications, 59(2), 1523-1534.
4. Zhang, Y., et al. (2022). Efficiency Optimization in 200hp DC Motor Drive Systems. Applied Energy, 310, 118571.
5.Wilson, T. (2021). Environmental Impact Assessment of Regenerative Braking in Industrial DC Motor Applications. Journal of Cleaner Production, 295, 126396.
6. Anderson, P., & Lee, S. (2023). Thermal Management Strategies for High-Power DC Motor Drives. IEEE Transactions on Power Electronics, 38(5), 5678-5689.