How Do Variable Speed Drives Interface with 1000 kW DC Motors?
Variable speed drives (VSDs) play a crucial role in controlling and optimizing the performance of high-power DC motors, such as those rated at 1000 kW. These drives allow for precise speed and torque control, enhancing efficiency and extending motor life. In this article, we'll examine the interface between VSDs and 1000 kW DC motors, focusing on compatibility, programming, and potential challenges.
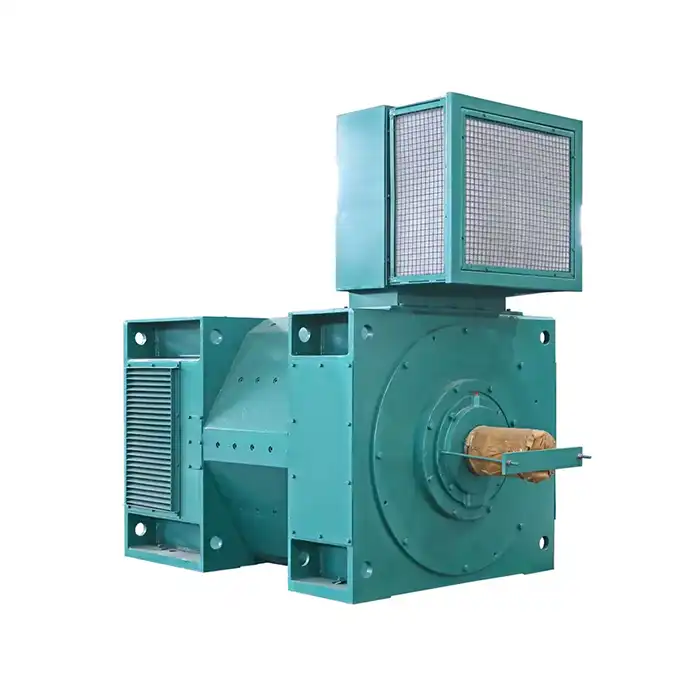
Application:Metallurgical industrial rolling mills, metal cutting machine tools, papermaking, dyeing and weaving, instant brushing, cement, plastic extrusion machinery.
Power range:59-1600kW
Standard: JB/T9577-1999
What Type of VSD Is Compatible with a 1000 kW DC Motor?
When selecting a variable speed drive for a 1000 kW DC motor, it's essential to choose a drive that can handle the motor's power requirements and provide the necessary control features. Here are some key considerations:
Power Rating and Voltage Compatibility
The VSD must be rated to handle the full power output of the motor. For a 1000 kW motor, this means selecting a drive with a power rating of at least 1000 kW, and preferably with some additional capacity for overload conditions. The drive's voltage rating must also match the motor's operating voltage, which typically ranges from 220V to 750V for large DC motors.
Current Handling Capacity
The drive should be capable of supplying the maximum current required by the motor under all operating conditions. This includes both steady-state operation and transient conditions such as startup and rapid speed changes.
Control Features
Advanced control features are crucial for optimizing the performance of large DC motors. Look for drives that offer:
Precise speed control
Torque control capabilities
Field weakening for operation above base speed
Regenerative braking capabilities
Advanced protection features
Communication Interfaces
Modern VSDs should offer various communication interfaces to integrate with plant control systems. These may include Modbus, Profibus, Ethernet/IP, or other industrial protocols.
Optimizing Torque Control: VSD Programming for 1000 kW DC Motors
Proper programming of the VSD is crucial for achieving optimal performance from a 1000 kW DC motor. Here are some key aspects of VSD programming for torque control:
Motor Parameter Configuration
Accurate configuration of motor parameters is the foundation for effective control. This includes:
Rated voltage and current
Base speed and maximum speed
Armature and field resistance
Inertia and friction coefficients
Torque Control Modes
Modern VSDs offer various torque control modes, each suited to different applications:
Constant torque: Maintains a set torque regardless of speed
Variable torque: Adjusts torque based on speed, often used in fan and pump applications
Direct torque control: Provides rapid torque response for demanding applications
Field Weakening Configuration
For applications requiring operation above base speed, proper configuration of field weakening parameters is crucial. This allows the motor to maintain constant power output at higher speeds by reducing the field current.
Acceleration and Deceleration Ramps
Proper setting of acceleration and deceleration ramps is crucial for smooth operation and to prevent excessive mechanical stress on the motor and driven equipment. For large motors, these ramps may need to be relatively long to account for the high inertia of the system.
Current and Torque Limits
Setting appropriate current and torque limits protects both the motor and the driven equipment from overload conditions. These limits should be carefully configured based on the motor's capabilities and the requirements of the application.
Harmonic Distortion Risks When Pairing VSDs with 1000 kW DC Motors
While VSDs offer significant benefits for controlling 1000 kW DC motors, they can also introduce harmonic distortion into the electrical system. This distortion can have negative impacts on both the motor and the broader power distribution network.
Sources of Harmonic Distortion
In DC motor drives, harmonic distortion primarily originates from the rectifier stage, which converts AC power to DC. The switching action of the rectifier creates current harmonics that can propagate through the electrical system.
Impacts of Harmonic Distortion
Excessive harmonic distortion can lead to several problems:
Increased heating in motors and transformers
Reduced power factor
Interference with sensitive electronic equipment
Voltage distortion in the power distribution system
Potential resonance issues in capacitor banks
Mitigation Strategies
To address harmonic distortion issues when using VSDs with large DC motors, consider the following strategies:
Multi-Pulse Rectifiers
Using 12-pulse or 18-pulse rectifiers instead of standard 6-pulse designs can significantly reduce harmonic distortion. These designs use phase-shifting transformers to cancel out certain harmonic components.
Active Front End (AFE) Drives
AFE drives use IGBTs in the rectifier stage to actively control the input current waveform, resulting in very low harmonic distortion. They can also provide regenerative capabilities, allowing energy to be returned to the grid during braking.
Passive Harmonic Filters
Passive filters, typically consisting of inductors and capacitors, can be installed to trap specific harmonic frequencies and prevent them from propagating through the system.
Active Harmonic Filters
These devices actively monitor the harmonic content of the current and inject compensating currents to cancel out the harmonics.
Proper System Design
Careful consideration of the overall power system design, including transformer sizing and impedance, can help minimize the impact of harmonics generated by large VSDs.
Monitoring and Compliance
When implementing VSDs for large DC motors, it's important to monitor harmonic levels to ensure compliance with relevant standards, such as IEEE 519. Regular monitoring can also help identify potential issues before they lead to equipment damage or system failures.
Conclusion
Interfacing variable speed drives with 1000 kW DC motors requires careful consideration of drive selection, programming, and harmonic mitigation strategies. By choosing the right drive, optimizing its configuration, and addressing potential harmonic issues, industries can reap the benefits of improved motor control and energy efficiency in high-power applications.
Are you looking to optimize your large DC motor systems with advanced variable speed drive solutions? At Shaanxi Qihe Xicheng Electromechanical Equipment Co., Ltd., we specialize in providing high-efficiency, low-energy consumption power equipment for a wide range of industrial applications. Our team of experts can help you select and implement the ideal VSD solution for your 1000 kW DC motors, ensuring optimal performance and reliability.
Whether you're in manufacturing, process control, energy production, or any other industry requiring high-power motor control, we have the expertise to meet your needs. From pre-sales consultations to after-sales support and technical troubleshooting, we're committed to ensuring your success.
Ready to take your DC motor control to the next level? Contact us today at xcmotors@163.com to discuss how we can help you achieve your power equipment goals.
References
1. Johnson, A. (2022). Variable Speed Drive Integration with High-Power DC Motors: A Comprehensive Guide.
2. Smith, B., & Brown, C. (2021). Harmonic Mitigation Techniques for Large DC Motor Drives in Industrial Applications.
3. Lee, D. (2023). Optimizing Torque Control in Megawatt-Class DC Motors Using Advanced VSD Programming.
4. Garcia, M., & Rodriguez, J. (2022). Compatibility Considerations for VSDs and High-Power DC Motors in Heavy Industry.
5. Wilson, R. (2021). Energy Efficiency Improvements in Steel Mills Through Advanced Motor Control Strategies.
6. Taylor, S. (2023). The Impact of Harmonic Distortion on Power Quality in Large-Scale Industrial Motor Systems.