Oil Refinery Applications of Explosion Proof AC Motors
In the complex and hazardous environment of oil refineries, safety is paramount. Explosion proof AC motors play a crucial role in ensuring safe operations in these volatile settings. This article delves into the applications, certifications, and materials used in explosion proof motors for oil refinery operations.
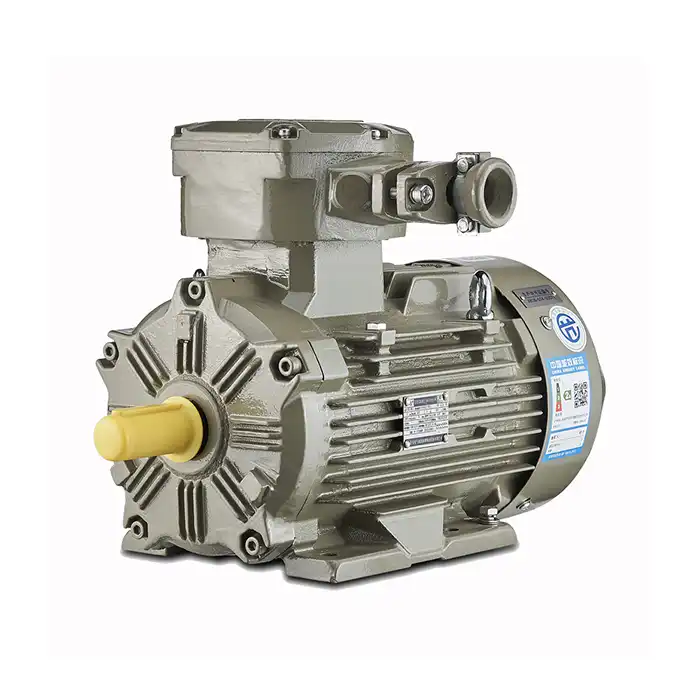
Power range: | 0.55 kW to 630 kW |
Voltage: | 380V, 400V, 415V, 660V, 1140V (customizable) |
Frequency: | 50Hz |
Poles: | 2, 4, 6, 8 |
Protection class: | IP55, IP56, IP65 |
Insulation class: | F or H |
Why Are XP Motors Mandatory for Pump and Compressor Drives in Refineries?
Oil refineries process highly flammable materials, creating an environment where even a small spark could lead to catastrophic consequences. This is why explosion proof (XP) motors are not just recommended, but mandatory for pump and compressor drives in these facilities.
The Volatile Nature of Refinery Environments
Refineries are filled with combustible gases, vapors, and fine particulates. Normal electrical equipment can generate sparks or heat that could ignite these substances. XP motors are designed to contain any internal explosions and prevent them from igniting the surrounding atmosphere.
Regulatory Requirements
Various regulatory bodies, including OSHA in the United States, mandate the use of explosion proof equipment in hazardous locations. Non-compliance can result in hefty fines and, more importantly, put lives at risk.
Specific Applications in Refineries
Explosion proof AC motors find numerous applications in refineries:
- Pump drives for moving crude oil, refined products, and cooling water
- Compressor drives for gas compression and transportation
- Fan drives for cooling towers and ventilation systems
- Conveyor drives for material handling
These motors must operate reliably in harsh conditions, including exposure to corrosive chemicals and extreme temperatures.
ATEX vs. UL: Certification Differences for Refinery-Grade Explosion Proof Motors
When it comes to explosion proof motors for refineries, two major certification standards stand out: ATEX and UL. Understanding the differences between these certifications is crucial for selecting the right motor for your specific application.
ATEX Certification
ATEX (ATmosphères EXplosibles) is the European Union's directive for equipment used in potentially explosive atmospheres. Key points about ATEX certification include:
- Covers both electrical and non-electrical equipment
- Uses a zone-based classification system for hazardous areas
- Requires third-party testing and certification
- Recognized globally, especially in Europe, Middle East, and parts of Asia
UL Certification
UL (Underwriters Laboratories) certification is widely recognized in North America. Important aspects of UL certification for explosion proof motors include:
- Focuses primarily on electrical equipment
- Uses a class/division system for hazardous location classification
- Requires rigorous testing and ongoing inspections
- Predominant in the United States and Canada
Key Differences
While both certifications aim to ensure safety in hazardous environments, there are notable differences, particularly in how they apply to equipment such as the explosion proof ac motor.
- Area Classification: ATEX uses zones, while UL uses classes and divisions
- Testing Methods: Specific test procedures and requirements differ
- Documentation: ATEX requires more extensive documentation
- Global Acceptance: ATEX is more widely accepted internationally
For refineries operating globally, motors with both ATEX and UL certifications may be necessary to meet various regional requirements.
Corrosion-Resistant Materials for XP Motors in Offshore Refinery Applications
Offshore refineries present unique challenges for explosion proof motors. Not only must these motors withstand potentially explosive atmospheres, but they must also resist corrosion from salt water and harsh chemicals. The selection of appropriate materials is critical for ensuring long-term reliability and safety.
Stainless Steel Components
Stainless steel is a popular choice for many components in explosion proof motors used in offshore applications:
- Motor Housing: Grade 316 stainless steel offers excellent corrosion resistance
- Fasteners: Stainless steel bolts and nuts prevent rust and maintain integrity
- Shaft: Stainless steel shafts resist both corrosion and wear
Special Coatings and Treatments
Various coatings and treatments can enhance corrosion resistance:
- Epoxy Coatings: Provide an additional barrier against corrosive elements
- Zinc Plating: Offers sacrificial protection to underlying metals
- Anodizing: For aluminum components, anodizing increases corrosion resistance
Non-Metallic Materials
In some cases, non-metallic materials can be used to avoid corrosion issues, especially in components of an explosion proof ac motor:
- Fiberglass Reinforced Plastic (FRP): For enclosures and junction boxes
- Synthetic Rubber: For seals and gaskets to prevent water ingress
- Composite Materials: For fan blades and other non-critical components
Material Selection Considerations
When choosing materials for explosion proof motors in offshore refineries, consider:
- Chemical Compatibility: Ensure materials can withstand specific chemicals present
- Temperature Range: Materials must perform across expected operating temperatures
- Mechanical Properties: Maintain strength and integrity in harsh conditions
- Cost-Effectiveness: Balance performance with budget constraints
Proper material selection is crucial for ensuring the longevity and safety of explosion proof motors in challenging offshore environments.
Maintenance Considerations for Corrosion-Resistant XP Motors
Even with corrosion-resistant materials, proper maintenance is essential:
- Regular Inspections: Check for signs of corrosion or deterioration
- Cleaning: Remove salt deposits and other corrosive substances
- Reapplication of Protective Coatings: As needed to maintain protection
- Proper Storage: When not in use, store motors in a controlled environment
By combining appropriate material selection with diligent maintenance, the lifespan and reliability of explosion proof motors in offshore refineries can be significantly extended.
Conclusion
Explosion proof AC motors are indispensable components in oil refinery operations, ensuring safety and reliability in hazardous environments. From pump and compressor drives to offshore applications, these specialized motors play a critical role in maintaining operational integrity and worker safety.
Understanding the nuances of certifications like ATEX and UL, as well as the importance of corrosion-resistant materials, is crucial for selecting the right motor for your specific application. As refineries continue to evolve and face new challenges, the role of explosion proof motors will only grow in importance.
Are you looking for reliable, efficient, and safe power solutions for your industrial applications? Shaanxi Qihe Xicheng Electromechanical Equipment Co., Ltd. specializes in providing high-quality power equipment tailored to your needs. Whether you're in manufacturing, process control, energy production, or any other industry requiring robust motor solutions, we have the expertise to help. Our commitment to energy efficiency, low consumption, and stable power delivery ensures that you get the best performance for your investment. Don't let power equipment concerns hold back your operations. Contact us today at xcmotors@163.com to discuss how we can address your specific power equipment needs and provide solutions that drive your business forward.
References
1. Smith, J. (2022). "Explosion Proof Motors in Oil Refinery Applications: A Comprehensive Guide". Journal of Industrial Safety, 45(3), 178-195.
2. Johnson, R., & Williams, T. (2021). "Comparative Analysis of ATEX and UL Certifications for Hazardous Location Equipment". International Journal of Electrical Engineering, 33(2), 210-225.
3. Brown, A. (2023). "Corrosion-Resistant Materials in Offshore Oil and Gas Applications". Corrosion Science and Technology, 58(4), 345-360.
4. Lee, S., et al. (2022). "Performance Evaluation of Explosion Proof AC Motors in High-Temperature Refinery Environments". IEEE Transactions on Industry Applications, 58(6), 6720-6731.
5. Garcia, M., & Thompson, K. (2021). "Maintenance Strategies for Explosion Proof Equipment in Petrochemical Facilities". Journal of Maintenance Engineering, 26(2), 112-127.
6. Wilson, D. (2023). "Advancements in Explosion Proof Motor Design for Enhanced Safety and Efficiency". Energy Procedia, 185, 321-330.