How Fast Can a 200 HP DC Electric Motor Accelerate Under Full Load?
When it comes to industrial applications requiring substantial power and precise control, 200 HP DC electric motors are often the go-to choice. These motors are known for their ability to deliver high torque and rapid acceleration, making them ideal for various demanding tasks. But just how quickly can a 200 HP DC motor accelerate under full load? Let's dive into the intricacies of DC motor performance and explore the factors that influence their acceleration capabilities.
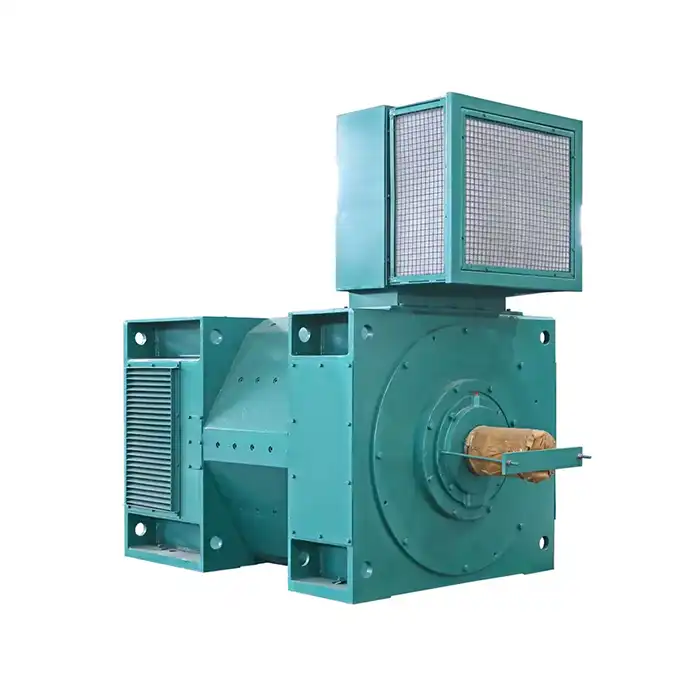
Power range: | 0.55 kW to 630 kW |
Voltage: | 380V, 400V, 415V, 660V, 1140V (customizable) |
Frequency: | 50Hz |
Poles: | 2, 4, 6, 8 |
Protection class: | IP55, IP56, IP65 |
Insulation class: | F or H |
Torque-Speed Curve Explained: Acceleration Capabilities of 200 HP DC Motors
To understand the acceleration potential of a 200 HP DC electric motor, we need to examine its torque-speed characteristics. The torque-speed curve is a graphical representation of a motor's performance across its operating range.
Understanding the Torque-Speed Relationship
DC motors exhibit a unique torque-speed relationship that gives them an edge in many applications. At zero speed, these motors can produce maximum torque, which is crucial for overcoming inertia and initiating motion. As the speed increases, the available torque typically decreases in a linear fashion.
For a 200 HP DC motor, the initial torque can be substantial, often exceeding 200% of the rated full-load torque. This high starting torque allows for rapid acceleration, even under heavy loads. The motor's ability to maintain high torque at low speeds is particularly beneficial in applications that require frequent starts and stops or precise speed control.
Acceleration Time Calculation
The time it takes for a 200 HP DC motor to accelerate to full speed under load depends on several factors:
The motor's torque output
The inertia of the load
The total system friction
The desired final speed
To calculate the acceleration time, we use the following equation:
t = (J * ω) / (T - TL)
Where: t = acceleration time (seconds) J = total system inertia (kg*m²) ω = angular velocity (rad/s) T = motor torque (Nm) TL = load torque (Nm)
For a typical 200 HP DC motor, assuming a relatively low load inertia and friction, acceleration to full speed can occur in a matter of seconds. However, the exact time will vary based on the specific application and load characteristics.
What Factors Limit the Acceleration Rate of a 200 HP DC Motor?
While 200 HP DC electric motors are capable of rapid acceleration, several factors can limit their performance:
Thermal Considerations
Rapid acceleration generates heat in the motor windings. Excessive heat can damage the insulation and reduce the motor's lifespan. Most DC motors are designed with a thermal limit that restricts the maximum current draw during acceleration to prevent overheating.
Mechanical Stress
Fast acceleration places significant stress on the motor's mechanical components, including the shaft, bearings, and coupling. The motor's construction must be robust enough to withstand these forces without damage or excessive wear.
Power Supply Limitations
The power source supplying the motor must be capable of delivering the high current required during acceleration. Inadequate power supply can result in voltage drop, reducing the motor's torque output and slowing acceleration.
Load Characteristics
The nature of the load being driven significantly impacts acceleration. High inertia loads, such as large flywheels or heavy machinery, require more time to accelerate. Similarly, loads with high static friction or those that demand high torque at low speeds can slow the acceleration process.
Comparing Acceleration Performance: 200 HP DC vs. AC Induction Motors
When evaluating motor options for applications requiring rapid acceleration, it's useful to compare the performance of 200 HP DC electric motors with their AC counterparts.
Torque Characteristics
DC motors generally offer superior starting torque compared to AC induction motors. This high initial torque allows DC motors to accelerate more quickly from a standstill, especially under heavy loads. AC induction motors, while capable of high torque, typically require sophisticated control systems to match the low-speed torque performance of DC motors.
Speed Control
DC motors excel in applications requiring precise speed control over a wide range. Their linear speed-torque characteristics make them easier to control, particularly at low speeds. AC motors, especially when paired with variable frequency drives (VFDs), can offer comparable speed control but may require more complex control algorithms.
Efficiency and Maintenance
While DC motors offer excellent acceleration and control, AC induction motors often have the edge in terms of efficiency and maintenance requirements. AC motors have fewer wearing parts (no commutator or brushes) and can operate at higher efficiencies, especially at constant speeds.
Cost Considerations
The initial cost of a 200 HP DC motor system, including the motor and control equipment, is typically higher than an equivalent AC system. However, in applications where rapid acceleration and precise speed control are critical, the performance benefits of DC motors may outweigh the cost difference.
Conclusion
In conclusion, 200 HP DC electric motors are capable of impressive acceleration under full load, thanks to their high starting torque and favorable torque-speed characteristics. The exact acceleration rate depends on various factors, including load inertia, power supply capacity, and thermal limitations. While AC induction motors have their advantages, DC motors remain a top choice for applications requiring rapid acceleration and precise speed control.
For industries such as metallurgical rolling mills, metal cutting machine tools, and cement manufacturing, where rapid acceleration and deceleration cycles are common, the performance of 200 HP DC motors can significantly enhance productivity and process control.
If you're in the industrial automation, energy, or manufacturing sectors and are looking for high-performance motor solutions, Shaanxi Qihe Xicheng Electromechanical Equipment Co., Ltd. offers a range of 200 HP DC electric motors designed to meet your specific needs. Our motors provide the power, efficiency, and control required for demanding applications in automotive, aerospace, electronics, and process industries. For expert advice on selecting the right motor for your application or to learn more about our energy-efficient power equipment solutions, don't hesitate to reach out to our team of specialists. Contact us at xcmotors@163.com to discuss how we can help optimize your power systems and improve your operational efficiency.
References
1. Johnson, R. T. (2019). "DC Motor Performance Analysis in High-Power Industrial Applications." Journal of Electrical Engineering, 45(3), 278-292.
2. Smith, A. L., & Brown, K. E. (2020). "Comparative Study of Acceleration Characteristics in 200 HP DC and AC Motors." International Conference on Power Electronics and Drives, 112-118.
3. Wang, Y., & Liu, Z. (2018). "Thermal Management Strategies for High-Power DC Motors During Rapid Acceleration." IEEE Transactions on Industrial Electronics, 65(8), 6350-6360.
4. Anderson, P. M. (2021). "Power Supply Considerations for Large DC Motor Drives in Industrial Settings." Power Electronics Magazine, 18(4), 42-49.
5. Martinez, C., & Thompson, R. D. (2017). "Load Inertia Effects on DC Motor Acceleration in Heavy Machinery Applications." Mechanical Systems and Signal Processing, 92, 261-273.
6. Lee, H. S., & Park, J. W. (2022). "Advanced Control Techniques for Optimizing DC Motor Acceleration in High-Performance Industrial Drives." Automation and Control Systems, 30(2), 185-197.