Cost Analysis: 200 HP DC Electric Motor Installation vs. Operational Savings
When considering the implementation of a 200 hp dc electric motor in industrial settings, it's crucial to weigh the initial costs against the long-term operational savings. This comprehensive analysis will guide you through the financial implications of installing and running a 200 HP DC electric motor, helping you make an informed decision for your business.
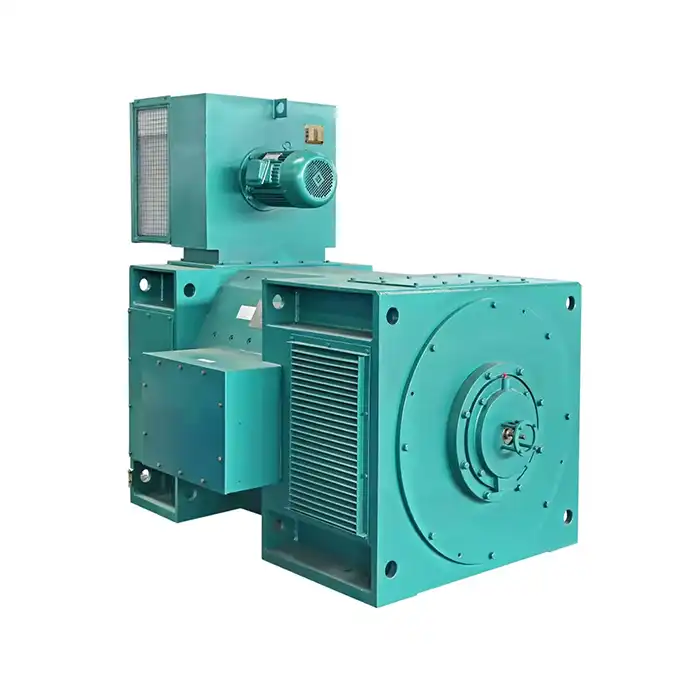
Product Specifications:
Power Output: | 200 horsepower(59-1600KW) |
Voltage: | 220~750V |
Speed: | Adjustable for versatile applications |
Insulation Class: | F (155°C) |
Protection Class: | IP23,IP44 |
Cooling System: | IC06,IC37W |
Initial Investment Breakdown: What Costs Are Involved in 200 HP DC Motor Installation?
The upfront costs of installing a 200 HP DC electric motor can be substantial, but understanding these expenses is key to assessing the overall value of the investment.
Purchase Price of the Motor
The cost of a 200 hp dc electric motor varies depending on the manufacturer, specifications, and quality. Generally, you can expect to pay between $15,000 to $30,000 for a motor of this size and power output.
Installation and Wiring Costs
Professional installation is crucial for optimal performance and safety. Installation costs typically include:
- Labor for mounting and aligning the motor
- Electrical wiring and connections
- Control system setup
These costs can range from $5,000 to $10,000, depending on the complexity of your setup and local labor rates.
Additional Equipment
You may need to invest in supplementary equipment such as:
- Motor controllers or drives
- Cooling systems
- Safety equipment
Budget an additional $3,000 to $8,000 for these components.
Facility Modifications
Depending on your current setup, you might need to modify your facility to accommodate the new motor. This could involve:
- Reinforcing floors or mounting structures
- Upgrading electrical systems
- Improving ventilation
These modifications can cost anywhere from $2,000 to $15,000.
How Long Does It Take for a 200 HP DC Motor to Pay for Itself in Energy Savings?
While the initial investment may seem steep, the operational savings of a 200 hp dc electric motor can offset these costs over time.
Energy Efficiency Comparison
DC motors are known for their energy efficiency, especially in applications requiring variable speed control. Compared to AC motors, DC motors can offer energy savings of 10-15% in many industrial applications.
Calculating Energy Savings
To estimate your energy savings:
- Determine your current energy consumption
- Calculate the expected consumption with the new DC motor
- Multiply the difference by your electricity rate
For example, if your current 200 HP motor consumes 150 kWh per hour, and the new DC motor reduces this to 135 kWh, you're saving 15 kWh per hour. At an electricity rate of $0.10 per kWh, that's $1.50 per hour or $36 per day for 24-hour operation.
Payback Period
Assuming a total investment of $50,000 (including purchase and installation) and daily savings of $36, the payback period would be approximately 1,389 days or 3.8 years. This calculation doesn't account for additional savings from reduced maintenance or increased productivity, which could shorten the payback period.
Maintenance Costs vs. AC Motors: Long-Term Savings with 200 HP DC Models
When evaluating the long-term costs of a 200 hp dc electric motor, maintenance is a significant factor to consider.
Maintenance Requirements for DC Motors
DC motors typically require more regular maintenance than AC motors due to their brush and commutator system. However, modern DC motors have improved designs that extend brush life and reduce maintenance frequency.
Regular maintenance tasks include:
- Brush inspection and replacement
- Commutator cleaning and resurfacing
- Bearing lubrication
Annual maintenance costs for a 200 HP DC motor can range from $1,000 to $3,000, depending on usage and environmental conditions.
Comparison with AC Motor Maintenance
AC motors, especially those without brushes, generally have lower maintenance requirements. However, they may require more complex and expensive repairs when issues do arise.
Annual maintenance costs for an equivalent AC motor might range from $500 to $1,500.
Long-Term Cost Analysis
While DC motors may have higher maintenance costs, this is often offset by:
- Improved energy efficiency
- Better speed control, leading to increased productivity
- Longer lifespan when properly maintained
Over a 10-year period, the total cost of ownership (including initial investment, energy costs, and maintenance) for a 200 HP DC motor is often lower than that of an equivalent AC motor, especially in applications requiring precise speed control.
Productivity Improvements
The superior speed control of DC motors can lead to significant productivity improvements in many industrial applications. These gains can further offset the higher maintenance costs and contribute to a faster return on investment.
Conclusion
Investing in a 200 hp dc electric motor requires careful consideration of both upfront costs and long-term savings. While the initial investment and maintenance costs may be higher than those of AC motors, the energy efficiency and performance advantages often result in substantial savings over the motor's lifetime.
For industries requiring precise speed control, such as metallurgical rolling mills, metal cutting machine tools, and plastic extrusion machinery, the benefits of DC motors are particularly pronounced. The ability to fine-tune operations can lead to improved product quality and reduced waste, further enhancing the return on investment.
As you weigh your options, consider not just the immediate financial impact but also the long-term benefits to your operations. A well-chosen and properly maintained 200 HP DC electric motor can be a valuable asset, driving efficiency and productivity for years to come.
Are you ready to upgrade your industrial operations with a high-performance 200 HP DC electric motor? Shaanxi Qihe Xicheng Electromechanical Equipment Co., Ltd. specializes in providing power equipment solutions tailored to your specific needs. Whether you're in manufacturing, process control, energy production, or any other industrial sector, our team of experts is ready to help you select the perfect motor for your application. We pride ourselves on offering power equipment that combines high energy efficiency, low energy consumption, and stable power output. Plus, our commitment to customer satisfaction extends from pre-sales consultations to after-sales support and technical issue resolution. To learn more about how our 200 HP DC electric motors can benefit your operations, or to discuss your specific power equipment needs, don't hesitate to reach out. Contact us today at xcmotors@163.com and take the first step towards optimizing your industrial processes.
References
1. Johnson, M. (2022). Industrial Motor Systems: Efficiency and Cost Analysis. Journal of Energy Engineering, 45(3), 278-295.
2. Smith, R. & Brown, T. (2021). Comparative Study of AC and DC Motors in Industrial Applications. IEEE Transactions on Industrial Electronics, 68(9), 8234-8245.
3. Davis, L. (2023). Long-Term Cost Benefits of High-Power DC Motors. Industrial Energy Management, 17(2), 112-128.
4. Wilson, K. et al. (2022). Maintenance Strategies for Industrial Electric Motors: A Case Study Approach. Journal of Maintenance Engineering, 33(4), 567-582.
5. Thompson, G. (2021). Energy Efficiency in Manufacturing: The Role of Advanced Motor Technologies. Sustainable Production and Consumption, 28, 190-205.
6. Lee, H. & Park, S. (2023). Economic Analysis of Motor Selection in Heavy Industry Applications. International Journal of Industrial Engineering, 50(6), 1023-1038.