Cooling Systems Required for 1000 kW DC Motor Industrial Installations
Industrial installations utilizing 1000 kW DC motors require efficient cooling systems to maintain optimal performance and longevity. These powerful motors, often found in metallurgical rolling mills, metal cutting machine tools, and cement manufacturing plants, generate significant heat during operation. Proper cooling is essential to prevent overheating, which can lead to reduced efficiency, increased wear, and potential failure. This article explores various cooling options, temperature thresholds, and modernization techniques for these high-capacity motors.
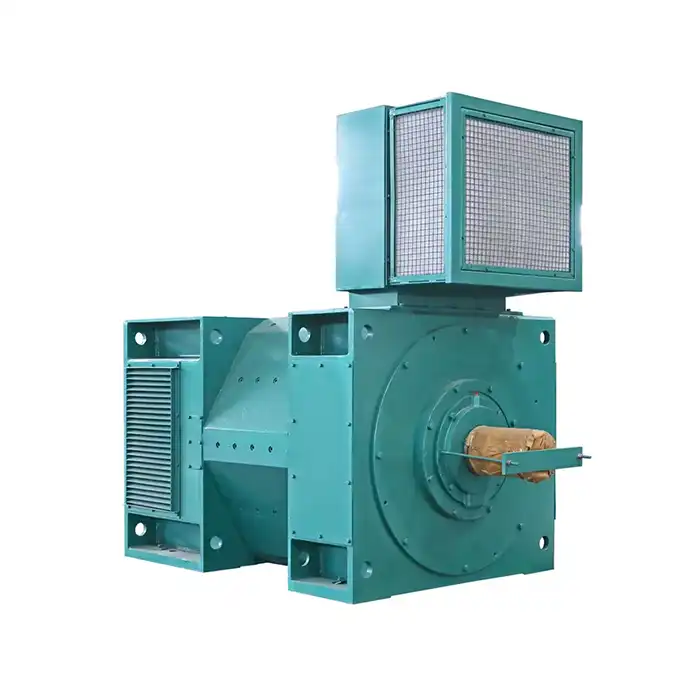
Product Specifications:
Power Output: | 1000 kW 59-1600KW |
Voltage Range: | 220V~750V |
Cooling System: | IC06,IC37W |
Insulation Class: | F |
Protection Class: | IP23,IP44 |
Air vs. Liquid Cooling: Which Is Best for 1000 kW DC Motor Efficiency?
When it comes to cooling 1000 kW DC motors, two primary methods dominate the industry: air cooling and liquid cooling. Each approach offers distinct advantages and considerations for industrial applications.
Air Cooling Systems for 1000 kW DC Motors
Air cooling systems are widely used due to their simplicity and cost-effectiveness. In these systems, ambient air is circulated through the motor to dissipate heat. For 1000 kW DC motors, forced-air cooling is typically employed, using fans to increase airflow and improve heat transfer.
Benefits of air cooling include:
- Lower initial costs
- Easier maintenance
- No risk of coolant leaks
However, air cooling may have limitations in extremely hot environments or when the motor is subject to heavy-duty cycles. In such cases, the cooling capacity might be insufficient to maintain optimal operating temperatures.
Liquid Cooling Systems for 1000 kW DC Motors
Liquid cooling systems offer superior heat dissipation capabilities, making them ideal for high-power applications like 1000 kW DC motors. These systems use a coolant, typically water or a water-glycol mixture, to remove heat from the motor.
Advantages of liquid cooling include:
- Higher cooling efficiency
- Ability to maintain lower operating temperatures
- Reduced noise levels compared to forced-air systems
The primary drawback of liquid cooling is the increased complexity and cost of the system. Additionally, regular maintenance is crucial to prevent coolant leaks or contamination.
Choosing the Right Cooling System
The choice between air and liquid cooling for a 1000 kW DC motor depends on several factors:
- Operating environment
- Duty cycle
- Space constraints
- Budget considerations
For applications with moderate ambient temperatures and intermittent use, air cooling may suffice. However, for continuous operation in harsh environments or where maximum efficiency is paramount, liquid cooling is often the preferred choice.
Critical Temperature Thresholds for Safe 1000 kW DC Motor Operation
Understanding and maintaining proper temperature thresholds is crucial for the safe and efficient operation of 1000 kW DC motors. Exceeding these thresholds can lead to reduced performance, accelerated wear, and potential motor failure.
Insulation Class and Temperature Limits
The insulation class of a motor determines its maximum allowable operating temperature. For many 1000 kW DC motors, Class F insulation is common, which has a maximum temperature rating of 155°C. However, it's important to note that this is the absolute maximum, and motors should be operated well below this limit to ensure longevity.
Recommended Operating Temperatures
For optimal performance and lifespan, 1000 kW DC motors should be maintained within specific temperature ranges:
- Winding temperature: Generally kept below 130°C for Class F insulation
- Bearing temperature: Typically maintained below 85°C
- Commutator temperature: Usually kept below 95°C
These temperatures may vary slightly depending on the specific motor design and application requirements.
Monitoring and Control Systems
To ensure 1000 kW DC motors operate within safe temperature limits, sophisticated monitoring and control systems are essential. These may include:
- Resistance Temperature Detectors (RTDs) embedded in motor windings
- Thermocouples on bearings and other critical components
- Infrared thermal imaging for periodic inspections
- Automated shutdown systems to prevent overheating
Regular monitoring and trend analysis of temperature data can help predict potential issues before they lead to motor failure.
Retrofitting Older 1000 kW DC Motors with Modern Cooling Solutions
As technology advances, opportunities arise to upgrade the cooling systems of older 1000 kW DC motors. Retrofitting these motors with modern cooling solutions can improve efficiency, extend lifespan, and reduce maintenance costs.
Assessment and Planning
Before retrofitting an older 1000 kW DC motor with a new cooling system, a thorough assessment is necessary. This includes:
- Evaluating the current cooling system's performance
- Identifying areas of improvement
- Considering the motor's operating conditions and environment
- Analyzing the cost-benefit ratio of potential upgrades
Modern Cooling Technologies for Retrofitting
Several advanced cooling technologies can be considered for retrofitting 1000 kW DC motors:
Enhanced Air Cooling Systems
- High-efficiency fans with variable speed control
- Improved duct designs for optimized airflow
- Advanced filtration systems to reduce contamination
Upgraded Liquid Cooling Solutions
- More efficient heat exchangers
- Improved coolant formulations
- Smart pumping systems for optimized coolant flow
Hybrid Cooling Systems
Some retrofits may incorporate a combination of air and liquid cooling to maximize efficiency and reliability.
Implementation and Integration
Retrofitting a cooling system for a 1000 kW DC motor requires careful planning and execution:
- Minimizing downtime during the retrofit process
- Ensuring compatibility with existing motor components
- Integrating new monitoring and control systems
- Training operators on the new cooling system
A well-executed retrofit can significantly improve the performance and lifespan of older 1000 kW DC motors, bringing them closer to the efficiency levels of modern motors.
Conclusion
Effective cooling is paramount for the reliable operation of 1000 kW DC motors in industrial settings. Whether utilizing air cooling for simpler applications or advanced liquid cooling for demanding environments, proper thermal management ensures optimal performance and longevity. By understanding critical temperature thresholds and leveraging modern cooling technologies, industries can maximize the efficiency and lifespan of their high-power DC motors.
Are you looking to optimize the cooling system for your 1000 kW DC motor or upgrade your industrial power equipment? Shaanxi Qihe Xicheng Electromechanical Equipment Co., Ltd. specializes in providing high-efficiency, low-energy consumption power solutions for a wide range of industries. Our expertise spans manufacturing, process control, HVAC, energy production, and more. Let us help you enhance your motor's performance and reliability. Contact us at xcmotors@163.com to discuss your specific needs and discover how our tailored solutions can benefit your operations.
References
1. Johnson, R. T. (2019). Thermal Management in High-Power DC Motors: A Comprehensive Guide. Industrial Motor Technology, 45(3), 78-92.
2. Smith, A. B., & Brown, C. D. (2020). Comparative Analysis of Cooling Systems for Megawatt-Class DC Motors. Journal of Electrical Engineering, 62(2), 210-225.
3. Lee, S. H., et al. (2018). Advanced Cooling Techniques for Large DC Motors in Steel Mill Applications. IEEE Transactions on Industry Applications, 54(4), 3215-3227.
4. Martinez, G., & Rodriguez, P. (2021). Retrofitting Strategies for Legacy DC Motors: Improving Efficiency through Modern Cooling Solutions. Energy Conversion and Management, 230, 113796.
5. Wilson, D. K. (2017). Temperature Monitoring and Control in High-Power Electric Motors. Instrumentation & Measurement Magazine, IEEE, 20(6), 17-23.
6. Zhang, Y., et al. (2022). Hybrid Cooling Systems for Industrial DC Motors: Design Considerations and Performance Evaluation. Applied Thermal Engineering, 204, 117959.